The Long-Term Risks of Neglecting Concrete Spalling in Commercial Structures
- Coastal Reconstruction Group
- 2 minutes ago
- 7 min read
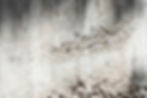
Concrete spalling might seem like a minor surface imperfection, but it’s actually an early warning sign of deeper structural problems—especially in Florida’s demanding climate. Left unaddressed, spalling concrete can escalate into a serious hazard for commercial properties, threatening pedestrian safety, causing code violations, and triggering costly foundation repairs.
In this article, we’ll examine how concrete spalling forms, why it’s so prevalent in Florida, and what property managers, engineers, and business owners need to know to protect their investment with proactive concrete repair and maintenance strategies.
What Is Concrete Spalling and Why Does It Happen?
Spalling occurs when the surface of reinforced concrete begins to break away, flake, or delaminate. This exposes internal materials—especially rebar and steel reinforcement—to moisture, air, and salt, accelerating corrosion and further degrading the substrate. Spalling is not just a cosmetic issue. It weakens the bond between concrete and metal, compromises flexural strength, and reduces the integrity of foundational systems such as parking decks, slabs, and balconies.
Common Causes of Spalling in Florida Commercial Buildings
Moisture Intrusion
Florida’s high humidity, rainfall, and poor drainage systems make moisture infiltration a common problem in commercial basements, sidewalks, and parking structures. Once water penetrates concrete cover, it interacts with calcium hydroxide and other compounds, triggering chemical reactions that expand the volume inside and cause internal pressure—leading to cracks and surface delamination.
Rebar Corrosion from Salt Air
Salt-laden air from coastal winds carries chloride ions that penetrate porous concrete. These chlorides attack the protective oxide layer around steel rebar, initiating a corrosion process that expands and breaks apart surrounding material. This is a major contributor to spalling damage along coastal highways, roofs, and multilevel decks.
Poor Installation or Aging Concrete
Improper formwork, inadequate concrete cover, lack of air entrainment, or inferior mix design can leave concrete vulnerable to wear and tear. Older structures, especially those with alkali-reactive aggregates or low pH values, are more susceptible to carbon dioxide infiltration and carbonation—processes that reduce alkalinity and promote rust and spall formation over time.
Where Spalling Typically Appears
Parking Garages
Elevated decks, ramps, and joint areas in garages endure constant exposure to water, abrasive vehicle traffic, and deicing chemicals. These conditions erode coatings, allow infiltration, and wear down expansion joints—causing progressive concrete failure.
Balcony Slabs
Balconies experience weather extremes, making them prone to thermal stress, freeze-thaw cycles (especially in North Florida), and water damage. Spall typically begins at corners or railing connections where waterproofing may have failed.
Building Facades
Cracking, staining, and spall on exterior concrete walls indicate moisture penetration and carbonation. These issues degrade aesthetic appeal, weaken structural capacity, and may release falling debris—posing risks to pedestrians below.
Structural Columns and Beams
Concrete spalling in load-bearing members like columns and beams is especially dangerous. It indicates compromised reinforcement, loss of flexural capacity, and potential failure under load—requiring urgent inspection and epoxy or mortar patch repair.
The Hidden Dangers of Unrepaired Concrete Spalling
Spalled concrete is more than an eyesore—it’s a red flag for deeper, structural degradation. Ignoring early warning signs increases both the cost and complexity of future repairs.
Structural Integrity Risks
Spalling often means the rebar inside the concrete is corroding and expanding, which reduces flexural strength and bond capacity. If the concrete slab or column is critical to the building's load-bearing system, the resulting failure could compromise the entire foundation and require major concrete leveling or reconstruction.
Safety Hazards for Tenants, Visitors, and Staff
Spalling creates loose chunks of concrete, rusted metal, and slippery surfaces—especially on pedestrian pathways like sidewalks, patios, or floors. These tripping hazards can lead to injury, liability claims, or even OSHA violations if not remediated.
Legal Liability and Code Violations
Florida building code requires commercial properties to maintain structural safety and waterproofing systems. Unaddressed spalling may result in enforcement actions, tenant complaints, or failed inspections—especially in aging condominiums or public-facing properties like shopping centers and office buildings.
Escalating Repair Costs Over Time
Concrete deterioration accelerates once the substrate is exposed. What begins as a simple patch job can evolve into full-depth concrete repair, structural epoxy injection, or even cathodic protection systems to halt corrosion. Early intervention with proper adhesive, sealant, and drainage controls keeps costs manageable and avoids extensive downtime.
Florida’s Climate and Why It Accelerates Concrete Damage
Florida’s tropical and coastal environment presents unique challenges to concrete durability. Spalling in commercial buildings can occur faster here than in many other parts of the country due to a combination of environmental stressors.
Salt Air, Humidity, and Rainfall Exposure
High humidity and frequent rain saturate porous concrete, increasing its permeability and accelerating chloride ion infiltration. In coastal zones, salt-laden air promotes steel corrosion beneath the surface, especially in exposed decks, walkways, and rooftop slabs.
Hurricane Winds and Coastal Conditions
Strong winds and driving rain during hurricane season stress both the structure and protective coatings. This often leads to cracks and water infiltration that undermine previous waterproofing or sealant systems—especially when concrete has poor air entrainment or substandard drainage.
Expansion, Contraction, and Freeze/Thaw Cycles (in North Florida)
While South Florida rarely experiences freezing temperatures, buildings in Central and North Florida do encounter occasional freeze/thaw cycles. These cause trapped water to expand and contract within the concrete matrix, leading to increased pressure, flaking, and surface failure.
How to Identify Early Warning Signs of Spalling
Staying alert to visible and subtle signs of concrete distress can help you catch problems early and avoid structural compromise.
Visual Clues on Walls, Ceilings, or Beams
Discoloration, flaking paint, and uneven surfaces on concrete walls, ceilings, or structural elements may indicate trapped moisture or internal corrosion. Tap tests using a hammer can reveal hollow-sounding areas beneath the surface.
Rust Stains or Flaking Concrete Near Rebar
If you notice orange-brown stains running down walls or columns, rust is likely forming around embedded rebar. As this steel expands due to corrosion, it exerts pressure on the surrounding cement, causing the outer layers to spall.
Cracking, Bulging, or Pitting Surfaces
Cracks or pits that develop without any known impact are early signs of spalling. Bulging surfaces may indicate internal corrosion or volume expansion of rebar due to carbonation or chloride infiltration.
Moisture Leaks or Damp Concrete Areas
Unusual damp spots on floors or ceilings could be caused by water infiltration from deteriorated concrete. Poor drainage or pressure buildup from ground moisture can compromise even sealed concrete slab areas.
The Concrete Spalling Repair Process in Florida
Addressing spalling requires a detailed and methodical repair process to ensure structural integrity, aesthetics, and code compliance.
Structural Assessment and Damage Mapping
The first step is a full inspection by a structural engineer or concrete repair expert. They will map areas of delamination, spall depth, and substrate condition using tools like thermal imaging or moisture meters.
Rebar Exposure and Corrosion Treatment
Exposed reinforcement is cleaned with a wire brush or abrasive blasting to remove rust and oxide buildup. In some cases, anode protection or cathodic protection is applied to prevent future corrosion.
Surface Cleaning, Patching, and Coating Systems
Loose concrete and dust are removed to expose a clean bonding surface. Technicians then apply patching mortar or polymer-modified concrete to rebuild the profile. A cementitious or epoxy-based bonding adhesive ensures strong adhesion to the substrate.
Waterproofing and Protective Sealants for Longevity
To prevent future moisture infiltration, the repaired area is coated with sealants or a waterproof membrane. Some systems also apply breathable paint or anti-carbonation coatings to limit chloride and carbon dioxide exposure.
Why Professional Repair Matters for Commercial Properties
A quick cosmetic patch might hide the problem temporarily, but long-term durability requires expert diagnosis and proper repair techniques.
Ensures Code Compliance and Structural Safety
Licensed contractors and engineers understand Florida building codes and local municipal inspection requirements. Professional repairs help you avoid fines, project delays, and insurance denials.
Prevents Business Disruption and Tenant Complaints
Timely repairs minimize hazards like falling debris, water leaks, and unsightly damage that can cause operational issues or impact tenant satisfaction.
Preserves Property Value and Curb Appeal
Spalled concrete on visible areas like driveways, walkways, or facades affects first impressions. Professional repairs restore your property’s clean look and prevent structural devaluation.
Supports Insurance Claims and Legal Protection
Comprehensive documentation, including before-and-after photos, moisture testing, and repair receipts, provides support for insurance claims or defense against liability claims tied to injury or property damage.
Coastal Reconstruction Group: Florida’s Concrete Spalling Experts
Trusted by Property Managers, HOAs, and Commercial Landlords
Coastal Reconstruction Group partners with commercial real estate leaders throughout Florida to deliver expert concrete repair solutions that prioritize safety, aesthetics, and longevity.
Experience in Multi-Story, Retail, and Hospitality Buildings
From high-rise condos to shopping centers and beachfront resorts, Coastal understands the structural demands and environmental pressures on a wide range of commercial properties.
Full-Service Structural Repair and Envelope Restoration
In addition to concrete spalling repair, Coastal offers full envelope restoration, foundation repair, drainage solutions, and waterproofing to provide a lasting defense against the elements.
Conclusion: Address Concrete Spalling Before It Spreads
Concrete spalling isn’t just a cosmetic concern—it’s a structural warning. In Florida’s moisture-rich, salt-laden, and storm-prone environment, early detection and professional repair are critical to preventing severe damage, costly liability, and business disruption.
Ignoring the signs today could lead to foundation failure, falling debris, and expensive lawsuits tomorrow. With expert help and preventative maintenance, your property can remain safe, code-compliant, and built to last.
Get Expert Concrete Spalling Repair in Florida
If you’ve noticed cracking, flaking, or rust stains on your commercial property’s concrete surfaces, don’t wait for the damage to spread. Coastal Reconstruction Group offers expert inspections, durable repair solutions, and full envelope protection tailored to Florida’s climate.
Our team includes licensed contractors and engineers with decades of experience in structural repair and restoration. We provide detailed damage assessments, waterproofing services, and long-term maintenance planning for commercial buildings of all types.
Contact us today for a consultation and discover how Coastal can help restore and protect your structure from the inside out—before small issues become major risks.
FAQs (Frequently Asked Questions)
What is concrete spalling, and why is it common in Florida?
Concrete spalling is the flaking, cracking, or breaking away of concrete surfaces due to moisture intrusion, steel rebar corrosion, or freeze/thaw cycles. In Florida, high humidity, salt air, and heavy rainfall accelerate spalling, especially in coastal and commercial environments where waterproofing or drainage may be inadequate.
Is concrete spalling a structural risk for commercial buildings?
Yes. If left unrepaired, spalling can expose and degrade steel reinforcement, reduce concrete cover, and compromise the structural integrity of slabs, beams, columns, and facades. Prompt concrete spalling repair is essential to maintaining safety, code compliance, and long-term building performance.
How do I know if my commercial property needs concrete spalling repair?
Warning signs include visible cracks, flaking concrete, rust stains, damp areas, or hollow-sounding surfaces. Spalling often appears near balconies, parking decks, facades, and columns. A structural inspection or moisture mapping service can confirm the extent of the damage.
What does the concrete spalling repair process involve?
The process typically includes structural assessment, removal of damaged material, rust treatment on exposed rebar, patching with mortar or epoxy, and applying waterproof sealants. In Florida, it’s also important to restore drainage and protect against salt intrusion for long-term durability.
Why should I hire a professional contractor for concrete spalling repair in Florida?
Concrete repair in commercial buildings must follow strict building codes, safety standards, and environmental considerations. A licensed Florida contractor like Coastal Reconstruction Group ensures your repairs are structurally sound, code-compliant, and built to withstand Florida’s harsh coastal conditions.